Die Casting Service: Revolutionizing Manufacturing Processes
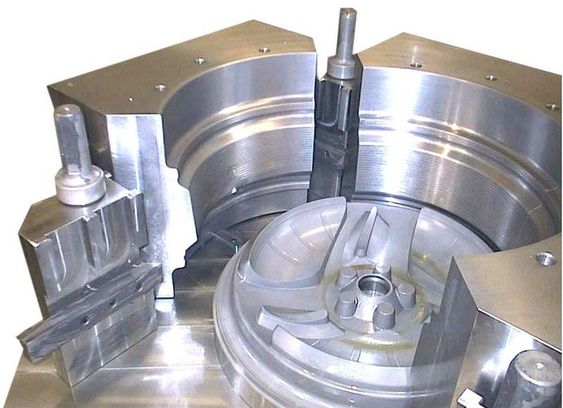
Introduction
In today’s manufacturing landscape, efficiency, precision, and cost-effectiveness are paramount. One technology that stands out for meeting these demands is die casting service. This article explores the intricacies of die casting service, its benefits, applications, and considerations for choosing the right service provider.
What is Die Casting?
Die casting is a manufacturing process where molten metal is injected into a mold cavity under high pressure. Once the metal solidifies, the mold is opened, revealing the finished die casting service product. This method is ideal for producing complex, high-precision parts with minimal post-processing required.
Types of Die Casting
Pressure Die Casting
Pressure die casting involves injecting molten metal into a steel mold cavity at high pressure. This method is suitable for producing intricate parts with excellent surface finish and dimensional accuracy.
Gravity Die Casting
Gravity die casting relies on gravity to fill the mold cavity with molten metal. It is commonly used for larger parts and offers cost-effective production solutions.
Low-Pressure Die Casting
Low-pressure die casting employs low pressure to fill the mold cavity with molten metal. This method is ideal for producing parts with thin walls and complex geometries.
Advantages of Die Casting
Die casting offers several advantages, including:
- High dimensional accuracy
- Excellent surface finish
- Thin-walled and intricate designs
- Cost-effective for large production runs
Applications of Die Casting
Die casting finds applications in various industries, including automotive, aerospace, electronics, and consumer goods. Common products produced through die casting include engine components, housings, brackets, and consumer electronics.
Die Casting Service Providers
Several companies specialize in providing die casting services, offering expertise in design, tooling, and production. Leading service providers include ABC Die Casting, XYZ Manufacturing, and Precision Castparts Corp.
Factors to Consider
When choosing a die casting service provider, consider factors such as:
- Experience and expertise
- Quality control measures
- Production capabilities
- Pricing and lead times
Quality Assurance
Quality control is critical in die casting to ensure the integrity and performance of the final product. Reputable service providers adhere to stringent quality standards and employ advanced inspection techniques to maintain consistency and reliability.
Cost Considerations
Die casting costs vary depending on factors such as material, complexity, and volume. It’s essential to evaluate pricing models and consider long-term costs, including tooling and post-processing expenses.
Future Trends
The die casting industry continues to evolve with advancements in technology and materials. Future trends include the adoption of sustainable practices, digitalization of production processes, and the development of lightweight alloys.
Case Studies
Several case studies highlight successful implementations of die casting service across different industries. From automotive components to medical devices, these examples demonstrate the versatility and effectiveness of die casting in modern manufacturing.
FAQs
- What is die casting service?
- How does die casting differ from other manufacturing methods?
- What are the advantages of die casting?
- How do I choose the right die casting service provider?
- What factors affect die casting costs?
- What are the future trends in die casting?
Conclusion
Die casting service plays a vital role in modern manufacturing, offering precision, efficiency, and cost-effectiveness. By understanding the process, applications, and considerations involved, businesses can leverage die casting to streamline production processes and stay competitive in today’s market.